.jpg?width=300&name=NavVis-point-cloud-refinery-1%20(1).jpg)
Oil and gas giant upgrades complex project planning with NavVis VLX
The company needed a faster way to capture 3D data at ground level in complex process facilities. Intertek suggested NavVis VLX, and the system delivered.
Executive summary
- A tier-one oil and gas company tested NavVis VLX at a dense, 30-acre process facility with “miles of pipes, tons of cable, steel, and major pieces of equipment”
- 3d laser scanner NavVis VLX was 5X faster than a terrestrial laser scanner (TLS)
- It also produced much cleaner, more precise data at ground level than UAVs
- The point cloud impressed the company’s engineers, integrated neatly with their existing workflows, and provided “real savings” for the business
- Since the test, the company has started to scale NavVis VLX across regions and departments, including operations
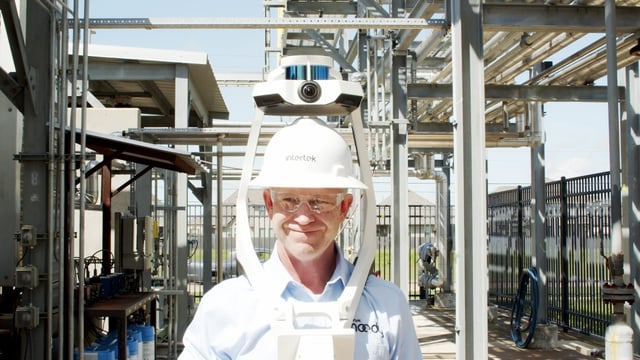
3D capture, quality assured
Intertek is a “quality assurance provider to industries worldwide,” explains business development rep Glen Kearns. In that role, the company supplies a range of services including comprehensive QA, testing, inspection, and even certification. And they work with leading companies in dozens of industries, from chemicals to construction, government to aerospace, healthcare, and manufacturing.
In his role at Intertek, Kearns specializes in 3D laser scanning services for oil and gas. One day, he received a call from a regular contact at a tier-one company. The company was looking for a new way to capture 3D data to create a digital plant of the as-built conditions in their expansive and complex process facilities.
.jpg?width=300&name=iStock-184802335%20(1).jpg)
Drilling down 3D data capture
This contact supports a group that performs what they call “pre-feed work,” which involves running alternatives analysis when the company adds equipment to existing facilities. Their jobs rely on comprehensive 3D data, which they use to test different equipment in the space, identify tie-in points, and perform in-depth route planning to help them with plant equipment relocation when the time comes.
This 3D data can be very challenging to capture.
Process facilities are remarkably complex. The contact explains, “Depending on the site, a refinery might cover 400 acres. And it will have hundreds and hundreds – if not thousands – of miles of dense piping cable, cable trays, structural steel, and major pieces of equipment. It’s dense and complex.”
The other issue is cost. “Since my team is doing preparatory work,” they say, “we have much smaller budgets than the teams that do detailed design and construction. So we need these scans quickly, we need them to be high quality, and need them done cheaply.”
Bring new plants to production quickly, confidently manage renovations, and minimize shutdowns by relying on accurate 3D data representation of your facilities
Moving on from traditional laser scanners
For a long time, this pre-feed team had hired service providers to perform terrestrial laser scanning (TLS) because “that was what was available at the time.” TLS was adequate for the task because it produced a dense, crisp 3D data set with high accuracy.
Kearns knows from experience that the complexity of these process facilities can make TLS capture very slow. “You have to plan out your scan, then set it up on a tripod, then capture, then do it over and over again,” he says. “You have to capture from a bunch of different angles” to ensure you get a good data set.
If you use TLS for capture, it can be difficult to cover the full site within the allotted timeline and budget. “There’s a finite number of locations where you can set the scanner up in a single day,” Kearns says. “If you try to get everything, you’ll be there forever.”
Terrestrial scanners also lack the maneuverability to get into the tight spaces common inside a processing facility. “If you’re scanning a congested area in a corner,” Kearns says, “or you need to get under a pipe or other occlusion, then you would need to take the scanner off the tripod and set it on the ground. It’s a real problem that you can’t get the tripod to go that low.”
As Kearns’ contact at the tier-one company explains, the data quality offered by TLS was not worth the time, effort, and expense. Especially since they didn’t need “nuts and bolts” accuracy for their alternatives analysis, tie-in identification, and route planning.
So they wanted Kearns and Intertek to help them find a better 3D laser scanning tool.
“Intertek has done a lot of scans for us around the world. But they’re not just our service providers, they’re our consultants. We’re very dependent on them because there are so many products out there I can’t test them all. We need Intertek to help us identify the best three tools, so we can test them and see which one fits our needs for the projects we’re working on.”
- Representative from Intertek's tier-one customer
Test flights
The first solution they tested was unmanned aerial vehicles (UAVs). These aerial capture platforms can be outfitted with photogrammetry or lidar payloads and then flown remotely. By capturing from above the complexity of the facility, UAVs offer a much faster workflow than TLS.
Kearns’ contact at the tier-one company decided to field test UAVs by capturing a cogeneration facility, which produces electricity and steam by burning natural gas through combustion turbines. “The facility we used is inside an oil field in California. It’s 30 acres of complex process areas, including towers and tanks that are 300 feet tall, miles of pipes, tons of cable, steel, and major pieces of equipment.”
And this test wasn’t just academic – it was for a real-world project. “We needed the data to plan for a brownfield expansion,” they say. “We’re building a carbon capture utilization and storage unit, so we needed to find tie-in points, so the unit could be connected to the existing facility. We also needed to do layout planning and route planning for all the new equipment we’re planning to build out there.”
As soon as they flew the UAVs and looked at the data, they knew that UAVs weren’t the full solution.
“They’re great for an overhead view. But when you get to the ground level, where the piping is complex, there’s no resolution. We call it the melted ice cream effect. It looks like everything is melted together. In order to get all the detailed data, we also needed a tool that could capture this facility at ground level.”
Enter SLAM scanning with NavVis VLX
As a laser scanning specialist for oil and gas, Kearns knew that simultaneous localization and mapping (SLAM) scanners could perform the ground-level capture his client needed.
These tools enable the technician to walk as they capture, which makes for very fast field execution. They are also handheld or wearable, which makes them very maneuverable for laser scanning in dense areas and around occlusions. The best SLAM scanners on the market even offer accuracy that rivals TLS scanning.
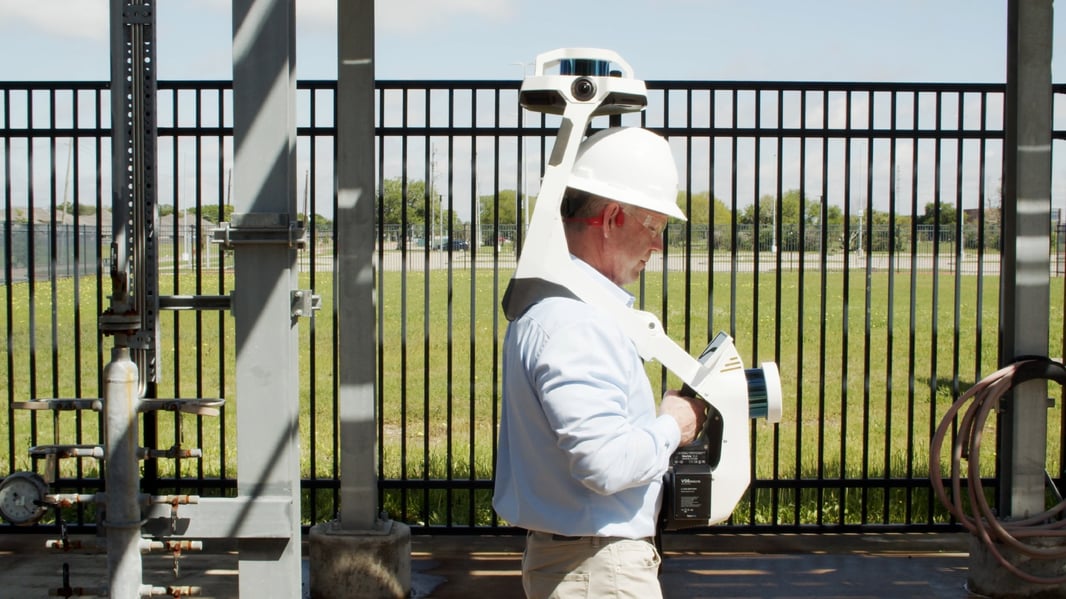
“There are a lot of SLAM scanners out there, and our client depends on us to find the best solution” says Kearns. “So we tested all the leading options. When we tested the NavVis VLX, it was the most versatile. The panoramic views were crisper and more photorealistic. And the overall density, precision, and resolution of the point cloud was the best. We showed the data to our contact, and we all agreed that NavVis VLX was the superior option for their needs.”
When Kearns’ contact tested the 3D wearable laser scanner at the cogeneration facility, it checked all the boxes for ground-level capture.
“SLAM scanning is new technology for us,” they say. “But we expected that NavVis VLX’s features and functionality would make it better than a tripod scanner for our application. We were right. And we estimated that we scanned the processed facility in 20% of the time it would have taken us with a tripod scanner.”
The SLAM workflow
Since that successful trial, Kearns and his team have used NavVis VLX to capture dozens of dense, complex process sites for their client. Here’s how.
First, the company supplies Intertek with drawings that identify the on-site monuments and benchmarks.
Next, Intertek sends a two-person team to the site with survey tools and NavVis VLX. One person starts the process by moving through the site and establishing survey control. They tie into the provided coordinates for the monuments and then set up the necessary control targets.
A little later, the next person starts moving through the facility capturing with the NavVis VLX laser scanner. “As they scan,” Kearns says, “they make sure that they capture an adequate number of targets using the on-board functionality. They also make sure to capture all the monuments, benchmarks, and tie-in points that the client needs for planning.”
.jpg?width=400&height=500&name=NavVis-VLX-3-CustomerValidation-3466%20(1).jpg)
Get the latest news as it happens by subscribing to the NavVis newsletter
Capture benefits
The first benefit of this NavVis VLX capture workflow is speed. Kearns says that Intertek can do a few hundred thousand square feet of a congested process facility in one day – including the survey. “You could not do that with a tripod-based scanner,” he jokes.
Kearns also says that Intertek’s 3D laser scanning team can capture around occlusions very easily when using NavVis VLX. “You can walk around with the scanner and get into dense parts of the facility very easily,” says Kearns. “You can maneuver the scanner into dense areas to get the equipment, the piping, and all the process areas from different perspectives and angles and approaches. You don’t have to worry about, 'Well, I only have time for 50 setups today, how am I going to get the data?'”
Despite this fast, fluid, and flexible workflow, Kearns says “the data is accurate and dense.”
“You don’t need the super-high accuracy of a tripod scanner for planning purposes, even in a complex process facility. You might give up a little bit of accuracy with a SLAM scanner, but at the end of the day, it generates an accurate, dense visual data set that you can use to visualize the site from all these different perspectives and collaborate for project planning and alternatives analysis.”
- Glen Kearns | Business Development Manager, Intertek
ROI of NavVis VLX
For Kearn’s tier-one client, these workflow benefits are not the main attraction of the NavVis VLX. “Remember that we don’t do the scanning ourselves,” they say. “So I’m not going to buy the hardware, I’m going to find a subcontractor like Intertek that can operate the scanner. Then I’ll hire them to do the work on my behalf as needed.”
That’s why the company judged the NavVis VLX on the data it produced, the post-capture workflow, and ROI.
“My engineers like the data,” Kearns’ contact says. “They felt like they were walking through the cogeneration facility themselves. Compare this to a TLS data set in bubble view, where they’re teleporting 100 or 200 feet at a time. That isn’t in an engineer’s comfort zone. They preferred NavVis VLX data because it enabled them to navigate and ‘walk’ through the facility seamlessly.”
Kearns says that he has found that flexibility is part of the system’s DNA. “They’ve done a great thing with that interoperability. It’s very helpful that all the data we collect with NavVis VLX can be viewed in other visualization tools.”
Due to this interoperability, the tier-one client can consider using NavVis VLX around the globe. “The company is in 100 countries,” Kearns’ contact says. “We have dozens of regions, and each might use a different set of software tools. Australia might use different visualization tools than Kazakhstan uses or different tools than North America uses, right? That’s why the flexibility offered by NavVis VLX is key.”
As for ROI and economic benefit, the contact says that NavVis VLX is already bringing “real savings.”
“It’s hard to prove a negative, to quantify all the money we didn’t spend,” they say. “But I get real savings every time I avoid sending a team of 12 engineers from Houston to Kazakhstan to do an engineering walk-down before a facility expansion. That’s expensive. With NavVis VLX, we can send the engineers a data set and have them work from the home office.”
Across the enterprise
Kearns’ contact stresses that he supports just one small group within this super-major oil and gas company. However, after NavVis VLX performed so well for his own group, he started to pitch the SLAM laser scanning system to other groups across the enterprise. And the device is catching on.
“I talked to colleagues in West Texas,” they say. “They are responsible for a lot of little processing units. Each one is just a few tanks a couple of pumps and some lines. But there are dozens and dozens – if not hundreds – of these things. And they’re very remote. They don’t like that they have to drive out just to take pictures and measurements.”
To solve this problem, Kearns’ contact recommended NavVis VLX. “The idea is that they can go out once, do these scans, and publish them. Then people in the home office can have access to them.” Rather than driving hundreds of miles for a simple piece of information, these professionals can pull up the data set in their home office and have the pertinent information at their fingertips.
“I also showed the tool to operations. They do a lot of turnarounds, which means shutting down parts of a plant to do extended maintenance. Turnarounds are expensive because the plant isn’t making products when it’s down. Every minute matters.”
Now, the company’s operations department is using NavVis VLX scans to do their own planning.
“They liked it because they could get their scan quickly, and their accuracy tolerance needs are like ours. They don’t need data down to the nuts and bolts level. The data from NavVis VLX helps them to do very detailed staging, so they can determine where they are going to move the equipment for maintenance ahead of time. That means faster turnarounds and less money lost.”
Laser scanning value at scale
As the contact notes, NavVis VLX is great for a variety of different applications across his tier-one oil and gas company. “The tool is the same in all these divisions and locations. It’s not useful just for one little organization like our engineering teams. We can use it in West Texas, we can use it in facilities, we can use it in operations. And these groups can extract different value from the tool than we do.”
“The ability of the NavVis VLX to scale is crucial for a company like us,” they conclude. “And that’s where the real value is.”
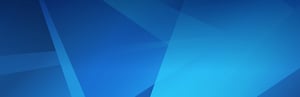