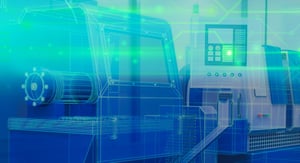
NavVis Digital Twin Use Cases
Get an overview of the use cases enabled by the NavVis Digital Factory Solution
Global manufacturing operations
When making decisions that are critical to your business, you’ll want to have all the latest information at your disposal.
This is the situation that a global operations manager and their team will find themselves in on a typical workday, presented with a multitude of choices spanning their entire production and sourcing network. Without the full picture, decisions take longer, and those delays can ripple outwards to impact productivity and efficiency.
But why are they required to make such choices in the first place?
One reason is the need to optimize the global production network because of shifting market demand or technological trends. A global operations manager will have to quickly evaluate the status quo and then initiate improvement and change projects.
Another reason is that, if they operate in a highly competitive market, there is inevitably pressure to lower production costs, shorten lead times and time-to-market for new products or a product refresh.
Finally, there are customers who expect not only that the products they buy should be of high quality, but that they should be easily available and with a retail price they find agreeable. Otherwise, they can easily take their business elsewhere...
Challenges to making effective decisions
A dynamic decision-making process is desirable to address all these factors and more besides, but there are challenges too. We’ve covered these in detail in the NavVis Digital Factory Guide, but to recap several:
- Production sites might be scattered all over the globe and share a very low level of standardization between them.
- Factory plans and documentation are woefully out of date, with no current or reliable overview of the factory inventory.
- Accessibility for all stakeholders is limited to those with the technical expertise to use CAD (computer-aided design) tools.
If you’re a global operations manager, then you might be familiar with the ways that these challenges can throw up roadblocks to progress.
Important decisions might be taken based on ill-informed opinions or “gut instinct”, made after protracted video conferencing with no real connection to the actual circumstances of the production environment.
Alternatively, you might be compelled to undertake a lot of traveling by plane, train and automobile to the site in question, an activity which can be expensive, time-consuming and stressful.
With the lack of a common understanding, teams reporting to a department head or a vice president can’t work together effectively. If email or instant messaging are your main channels of communication, then you’re in a for a protracted sequence of misunderstandings and communication loops.
What’s the solution?
But it doesn’t have to be this way. NavVis IVION Enterprise enables global operations managers to virtually inspect and compare their different production sites all over the world, all from within a web browser.
You won’t have to physically travel any more. You and your team can remotely visit a site to gain a complete understanding of machines, tools, and even entire factory layouts.
This empowers you to quickly make a qualified decision – in full confidence – without the need to be on-site. Saving time and expenses required for travel doesn’t hurt the bottom line, either.
In the scenario outlined in the video above, we simulate the acquisition of a new plant for manufacturing components. The global operations manager needs to inspect the new site and align with the local operations director. But before manufacturing can properly begin, some adjustments need to be made to the factory to align with the global production standards of its new owner.
The site is easily shared as a link directly from NavVis IVION Enterprise and added to a web meeting to discuss matters from within the factory's spatial context. This way, stakeholders can effortlessly gather all the critical information, then assess and swiftly resolve any engineering issues that may arise before the start of production.
The local operations director can also remotely access the digital twin of the respective lead factory, then make a visual comparison against the local site.
Taken together, the NavVis workflow and the digital factory twins enable a higher level of standardization, higher flexibility, and faster optimization in production. It is also a guaranteed means of reducing travel time and cost while simultaneously increasing the collaboration of all stakeholders such as logistics, industrial engineering, continuous improvement, and more.
If the goal in your organization is to have greater flexibility in production, not to mention fast optimization of your global production network, then look no further than NavVis IVION Enterprise.
As the manufacturing footprint of your company grows through mergers and acquisitions, you can anticipate the need for standardization. Reduce costly planning mistakes and make smarter decision based on the most current information available.
Equipment relocation
A standard practice in modern manufacturing is that production facilities are situated close to target markets or end-customers. But if your market is going through periods of volatility, where demand can suddenly rise and fall, production facilities need flexibility to allocate their manufacturing equipment.
To transfer resources within a global network, a central planning team will frequently evaluate their entire stock of machinery, e.g., large heavy equipment and assembly lines. The information they provide feeds into the logistics of transportation, organization, and installation of such equipment.
For this reason, planners need up-to-date CAD (computer-aided design) data of both the donor factory and the recipient. They’ll also need access to the latest documentation and evaluation on the condition of the equipment. And once the facility is disassembled, it's critical to know how to put it all back together at its destination!
Without proper documentation, planners may need to physically travel to the location to assess the status quo of the factory. If they can’t gather information in person, central planning teams may fall back on old and outdated 2D plans. This leads to further disruptions in operations and the delay of essential changes.
That’s where the NavVis Digital Factory Solution enters the picture. Using NavVis IVION Enterprise, 3D visualization software that's accessible from any standard web browser, factory planners have a powerful, easy-to-use tool to organize their assembly lines and install equipment.
Moving production closer to a high-volume customer
Let’s explore this particular use case through a detailed scenario; imagine that a CNC mill needs to be relocated to another factory so that production can be moved closer to a high-volume customer.
To begin, the measurement tool in NavVis IVION Enterprise enables users to quickly and reliably verify the space required for the machine by checking its physical dimensions at its current location – all from the comfort of their desk.
Once taken, the measurements and any other bits of relevant information can be attached to this specific location as geo-tagged content using the Points of Interest feature, together with a direct link to the new location in the recipient factory.
With this set of measurements readily available, the factory planner can now review the dimensions at the new site and confirm whether the CNC mill will comfortably fit without any issues.
Other considerations like ventilation ducts or electricity supply cables can be also be reviewed by studying the high-definition panoramic images from within NavVis IVION Enterprise.
The proposed location is then tagged with a shareable Point of Interest and linked back to the original location.
Another benefit of NavVis IVION Enterprise is the way it can deliver routing information from within a spatial context. Before taking a single step, the proposed routing for both stages of the equipment can be shared with internal and external stakeholders for inspection, together with all relevant information that will accelerate decision-taking.
3D data as high-quality point clouds
In addition to the immersive panoramic images, the NavVis Digital Factory Solution also consists of 3D data as high-quality point clouds.
NavVis IVION Enterprise has a popular feature where users can crop and download specific sections of their point cloud datasets as an E57 file. This selection can be sent directly to the relevant teams and imported into third-party applications for modeling and simulation.
Layout concepts can be verified quickly and smoothly without the need for extensive modeling, simply by introducing point clouds directly into CAD software. This is especially valuable when examining fitting feasibility, considering the equipment in the context of its surroundings, and bringing stakeholders into alignment before anything is moved.
What about other related tasks like document compliance, training for new machine operators at the new location, or repairing and replacing worn parts? These activities can also be supported by the immersive visualization of NavVis IVION Enterprise, thanks to a suite of features that enhance collaboration.
In this way, the NavVis Digital Factory Solution to relocate equipment helps to not only reduce planning and travel time, but also the cost of external relocation service providers, while at the same time eliminating the risk of planning mistakes that lead to costly disruptions to production, or delays in starting up the relocated machines.
Layout and assembly line planning
Making operational improvements to a manufacturing facility can be carried out for a multitude of reasons – to save time, reduce costs, optimize processes and decision-making, and more. And one of the core activities to achieve these benefits is optimizing their layout and assembly line planning.
The layout of a factory or production facility has a significant impact on day-to-day operations. How far do the raw materials have to travel from the building entrance to the production line? How close is the machinery to the necessary ventilation ducts, lighting, or power outlets? And once the finished product rolls off the line, how long before it reaches the QA bench, then loaded onto transport? All these factors are critical, and a poor layout has real consequences for the bottom line.
Broadly defined, “layout and assembly line planning” is the arrangement of all equipment, machinery, and furnishings within a factory, in accordance with a company’s performance goals. Typically, a Central Factory Layout or Assembly Line Planning Department – or Industrial Engineering Department – would subdivide the task into conceptualization, detailed planning, and execution.
Modern reality capture and visualization technologies like NavVis IVION Enterprise and the NavVis Digital Factory Solution can make the process of layout and assembly planning more effective than ever before. Especially concerning the conceptualization and detailed planning stages.
Why layout and assembly line planning is so important
Factory planners, project managers, and all other teams responsible for layout and assembly changes today need a dynamic, collaborative decision-making process.
The trigger for a change might be the introduction of new products and services, the need for space optimization, or switching up their output in accordance with changing market conditions. In the case of the automotive industry, for example, these events happen at an accelerated pace with car model derivatives.
Other reasons for assembly line changes might be a revision to start of production (SOP) or a product reaching end of production (EOP), but also optimization processes such as line balancing and continuous improvement.
Industrial engineers employed by the company are responsible for the planning and management of these change projects, and they’re typically carried out using external contractors.
Challenges facing factory layout and assembly planning today
One problem for project managers is when they must rely on outdated or incomplete documentation for their planning. The effort required to pull together existing paperwork from various sources can be a tremendous waste of time. It can also cause unnecessary mistakes and change requests, which in turn leads to longer planning cycles and overruns of the project budget.
Another issue occurs when planning is based on a top-down 2D perspective – like a basic floor plan – instead of a feature-rich model. Without the third dimension, it’s easy for important details to get left out, like the height to accommodate overhead installations, or access to power supplies.
Next is the question of how time-consuming and expensive the planning process can be if the onsite as-is status is required. Travel to and from the factory for site and equipment inspections can drag out the process into weeks and months, especially if the factory is in a remote location, or if there are restrictions on travel for health and safety concerns.
Rounding out our series of challenges for the weary factory planner are the data silos that exist between departments and factories, compounded by different 3D data tools, formats, and workflows.
Mark & Measure in NavVis IVION Enterprise levels up the layout and assembly planning workflow
In the scenario outlined in the video above, the factory planner needs to design a new layout regarding lean process improvement.
Here, a specific part of the plant must be remodeled in order to optimize material flow and space utilization, which would allow for an increase in production output for a given time. In NavVis IVION Enterprise, these areas can be identified and marked using a colorized overlay, uniquely named, and grouped into folders for even further clarity using the Mark & Measure tool.
Additionally, the 3D panoramic images in NavVis IVION Enterprise enable factory planners to remotely inspect the current usage and workplace set up in the specified area. Inspecting machine connections to the air, gas, and water supply allows for the planning of future machine requirements, especially when giving external contractors access to the virtual factory.
Once the production steps and workplaces are marked in NavVis IVION Enterprise as documentation of the current layout, the new and existing layouts can be easily compared. The factory planner can see that the new planned layout not only optimizes material flow, but also demonstrates where there is free space that could be used in the future to further increase production by installing an additional line.
When planning is complete, all related information and markups can be shared with colleagues via a web link or exported into an auto-generated PDF that includes the links to each markup, description of the workflow step, and related space usage. It’s really as simple as the click of a button!
NavVis IVION Enterprise enables all stakeholders to virtually inspect different layouts and communicate more efficiently with each other. Without having to physically travel, planners, managers, and teams can remotely visit sites to understand machines, tools, and even plan entirely new factory layouts. This empowers them to quickly make qualified decisions without the need to be on-site and make substantial savings on time and costs.
Best practice sharing
Let’s imagine that you’re a working on an assembly line in a factory. You’ve made an important discovery: moving a storage cabinet nearer to your workbench has improved your productivity by as much as 25%, because you don’t have to leave your spot to reach for the tools you use most often.
Naturally, your supervisor is delighted to hear this. They want to explore whether the same change can be applied elsewhere on the shop floor, or perhaps even in other production sites. If making such a simple change improves productivity for everyone else, the whole company benefits, so well done you!
Sharing best practices, of which the story above is a very simplified example, has great potential for increasing company productivity and efficiency. They can also mitigate errors and reinforce contingency planning. The critical thing is to document best practices fully and be able to share them easily.
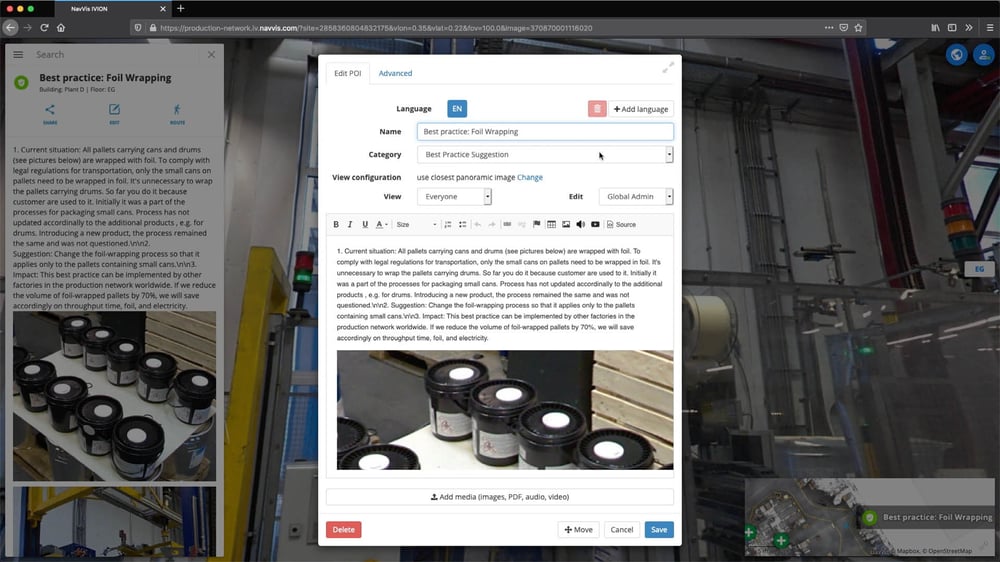
Enter the Continuous Improvement Manager
Responsibility for documenting a best practice will lie with Continuous Improvement (CI) Managers. In this role, a local CI Manager not only submits best practices of their facility to Central HQ, but they’ll also evaluate whether best practices shared by the head office can be implemented in their own facility.
Further up the chain, central CI teams must assess the ideas and proposals for best practices submitted to them from multiple sites. If they’re viable, then the team makes them available to other factories while providing support for implementation.
Sounds simple, doesn’t it? The challenge is that many valuable learnings too often go undocumented and aren’t communicated, because the processes of best practice sharing itself is too complex or time-consuming. Short-term productivity takes a dip if it takes a whole day to document a single best practice.
Another issue might be that, without a decent platform in place, there’s no way to standardize the inputs. Multiple text descriptions, pictures and 2D layouts presented in different formats and quality makes it too difficult for global CI teams to see the usefulness of a best practice.
There’s also the question of spatial context. The value of a proposed best practice mightn’t be apparent when taken out of the context of its physical location on the shop floor. For this reason and the ones mentioned previously, travel to the site might be the only way to get the full picture.
Best practice sharing with NavVis IVION Enterprise and NavVis IVION Go
There is a better way. NavVis IVION Enterprise and NavVis IVION Go are a unique pair of visual tools that enable anyone on the shop floor to present new ideas from within their spatial context. CI Managers can share best practice initiatives with a URL that's easy to access, understand and implement.
In the scenario in the video, the CI Manager of a factory would like to share a best practice guideline on a process for foil-wrapped goods. Using NavVis IVION Go, they can position themselves at the shop floor's relevant area and, from this exact location, compile a detailed report of the improvements achieved. They can even take photos – or add images from a library – to enrich the description.
Shop floor workers can also follow the same process to share locally tested and proven solutions with the global CI team.
Back at the head office, a global CI Manager uses NavVis IVION Enterprise to review the proposal from a standard web browser.
If the assessment is positive, these best practices become candidates for rollout across the global production network and shared with a central team of continuous improvement managers.
Example features:
- An intuitive overview of all sites allows CI managers to quickly access best practices at any location.
- Geo-tagged points of interest can present information as documents, images, videos, and more, making it easy for every stakeholder to access and share knowledge throughout the company.
- The search box provides users with a quick way to find documented improvements.
And that's a summary of how NavVis IVION Enterprise and NavVis IVION Go can enhance spatial awareness of factory layout in line with best practice sharing.
Now you can quickly and easily submit your proposal for a best practice and be rest assured that the recipients have all the information they need for a proper review.
Adding a spatial context streamlines the communication of ideas and improves the adoption rate of best practices across the global production network. It also leads to greater standardization, additional cost savings, and worldwide improvements to product quality.
Intuitive visual interface
Internet of Things (IoT) devices are featuring more and more prominently in industrial environments. The data they provide help us to make smart decisions about the status of the production line, operations, and myriad tweaks to boost operational efficiency.
Within a modern production facility, multiple streams of real-time data are being generated not just by IoT sensors, but also cameras, programmable logic controllers (PLC), and manufacturing execution systems (MES).
By collecting and analyzing this information across multiple sources, operations managers situated either locally or globally can better optimize the predictive failure reporting in their factories, thereby increasing productivity while reducing maintenance costs and time to resolution.
The status quo with IoT data gathering – and the bottlenecks
So how do these sensors work in practice? IoT devices are often discreetly installed and are not directly accessible to personnel on the factory floor.
The dashboards through which IoT and asset data is scrutinized have one glaring issue, however, and it concerns spatial intelligence. They don’t have enough information about the context and location of machinery, production lines, or processes. In other words, there’s no tangible link between the data being collected and the physical environment it’s situated in.
Another challenge is complexity. Planning, managing and analyzing a mountain of data in real time is an intricate task, usually limited to specialized personnel. A broader perspective of factory processes is not available at managerial levels, making the detection and communication of a problem more cumbersome.
What else? Well, if data is delivered through multiple platforms with no consideration for interoperability, each piece of intelligence is effectively siloed. It’s not altogether impossible to join the dots and make observations, but information retrieval and analysis takes far longer than it needs to.

Here, too, the omission of spatial context is felt. Without an intuitive way to pinpoint exactly where in the factory building or shop floor the data is coming from, how is it categorized and sorted? If we don’t know where these multiple data sources are coming from, we might overlook how they influence and relate to one another.
Spatial context provides the solution
The answer is to supplement IoT (and other smart devices installed at production plants) with positioning data. A dashboard with a visual interface containing spatial intelligence can present a unified data stream with multiple levels of granularity, ranging from the production network or the individual plant, right down to the shop floor or the machine itself.
Production planners and facility managers can access performance insights and identify areas and processes for improvements in real time within the context of factory space. And these insights needn’t be limited to a handful of personnel, but made available to every factory worker for better understanding and efficiency.
Using NavVis IVION Enterprise, for example, you can execute basic commands and controls directly. And you can compare the performance of similar areas in different production sites, identifying areas of commonality and scope for improvement. You could even establish a layout “benchmark” with the best performance and use that as the basis for setting up a new factory or production line.
In summary, by adding the spatial context to IoT sensors and their like, operations managers are empowered to make better decisions. Locative awareness supports planning, management and analysis.
Tasks like predictive maintenance are improved through a greater understanding of the environmental context. Other benefits might be a reduction in downtime, and an uptick in asset utilization and productivity. Standards are raised across the production network, without a spike in the effort required for coordination across sites, time-zones and countries.
Rolled out across multiple sites globally, a visual interface powered by NavVis IVION Enterprise will make a substantial contribution to operating margins.
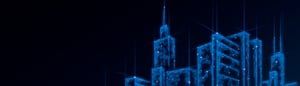
Book a free consultation to find out more
You're only a few clicks away from having every factory at your fingertips