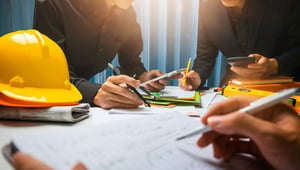
The impact of reality capture technology on Architecture, Engineering, and Construction:
The innovators’ perspective
Those Who Don’t Innovate – And Those Who Do
In the field of Architecture, Engineering, and Construction, there is a growing emphasis on efficiency, accuracy, and cost-efficiency. As projects become larger and more complex, traditional techniques and their practitioners sometimes struggle to meet the rising expectations and high standards of today.
This article examines the diverse aspects of architecture, engineering, and construction processes that have been impacted by recent innovations in reality capture, spotlighting companies that are changing the way we work through technological advancements.
These companies don’t just meet existing standards; they set new ones.
From the initial design phase to the final construction, and across a variety of project types and applications, we explore the many ways in which advanced reality capture technology improves project results, simplifies operations, and reduces costs. Let’s take a closer look at how innovators think.
Scanning, More Scanning, and More Than Scanning
We begin by breaking down the main different stages of a project and exploring the distinct benefits reality capture technology brings to each phase. Recognizing these strengths allows our innovators to utilize their technology strategically, leveraging the benefits on their projects. Here's how reality capture plays a pivotal role across different project phases.
In addition to project phases, keep reading for more insights into use cases.
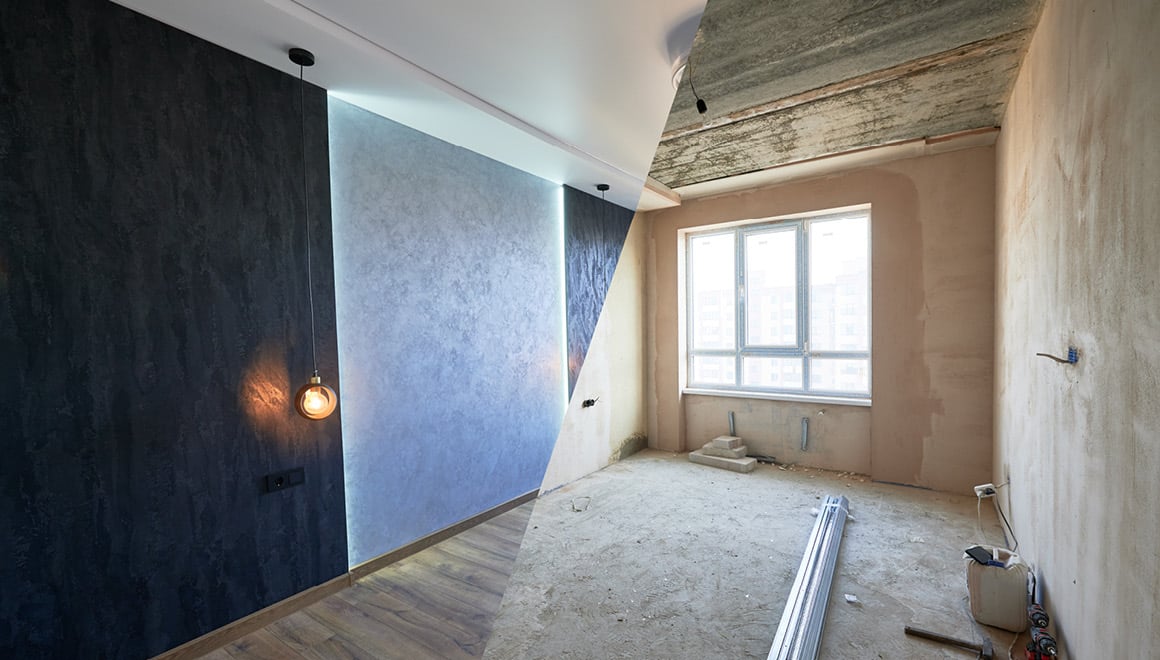
Design Phase
The early design phase, where the vision, scope, and specifications are established, forms the groundwork for any architecture or engineering project. Design serves as the basis for construction.
Reality capture technology can play a vital role at this stage, enabling accurate and comprehensive data collection, processing, and visualization. With the right scanning equipment and spatial data management platforms (NavVis VLX and NavVis IVION in particular), professionals can reliably capture the existing conditions of a site or structure to base their functional designs on—detailed designs that account for all the relevant factors and constraints.
Surveying a site during this phase not only saves time and money by reducing the need for manual measurements, but it also boosts trust in the quality and accuracy of the design, minimizing the need for later design changes or rework. Moreover, software solutions such as NavVis IVION facilitate collaboration and communication among project stakeholders, as different parties can easily share, view, and work on spatial data.
Construction Phase
This is when the plans become a reality.
At this stage, advanced reality capture technology allows for regular monitoring, verification, and adjustment of construction progress. By comparing the scanned data of the actual site or structure with the design model, professionals can detect and correct any deviations, discrepancies, or flaws that may arise during construction early on, reducing the need for costly, destructive rework.
Scanning to verify the true state of a construction site also helps comply with project specifications, standards, and relevant codes and regulations. This technology improves the safety and efficiency of workers, as they can access updated scanned data remotely, avoiding unnecessary trips and risks and maximizing their time onsite. Construction workers can, for example, check the most recent state of a site and see how to reach a specific location—often more complicated than it seems. Digitized spatial data also facilitate the documentation and access of health and safety measures, empowering superintendents, safety managers, and engineers to easily check if all the safety measures and precautions are in place.
Last but certainly not least—by allowing timely adjustments and preventing costly rework, and, as we will see below, by facilitating renovation planning and lifecycle management—reality capture can ultimately reduce waste and environmental impact, as it optimizes the use of materials and resources.
Post-Construction Phase
When the project is done, the work is inspected and handed over to the client.
If you’ve used advanced reality capture technology in the construction phase, you can provide reliable and comprehensive documentation such as as-built models that reflect the exact conditions of the final site. This spatial information can then be used for quality assurance, asset management, maintenance, and renovation purposes.
Scanning ensures satisfaction and builds trust, proving adherence to project requirements and expectations. If shared via user-friendly software platforms like NavVis IVION, the increased usage of such project data becomes one more value addition to your standard set of deliverables.
Explore the synergy between digitalization and reality capture.
Download our AEC industry survey report.
One for All
1. Construction Verification
Verification – including site inspection, quality assurance and control (QA/QC), and the identification of issues – is crucial when ensuring that architecture, engineering, and construction projects adhere to the highest standards of accuracy and quality from start to finish.
By conducting thorough surveys of job sites, professionals can generate detailed 2D/3D plans and lists of potential issues in a digital format. This method not only facilitates a comprehensive understanding of the site’s condition but also allows for the efficient communication of findings to all stakeholders involved.
The ability to categorize and address various issues identified during and after the scan is crucial. Some issues may be deemed minor and not require immediate action, while others might necessitate significant adjustments to the design plan and alterations on site. Integrating cost assessments for critical issues enables project managers, engineers, and customers to make informed decisions based on the potential impact on the project’s budget and timeline.
By improving the precision of site inspections and issue detection, scanning technology like NavVis VLX 3 provides significant economic benefits, helping to avoid expensive reworks and delays.
As an easy-to-use software platform for spatial data management, NavVis IVION enables team members—experts and novices alike—to perform verification tasks, thus increasing workflow efficiency and making better use of limited, specialized expertise in other areas.
"With the NavVis solution, we can conduct virtual site walks anytime, facilitating comparisons between drawings and the actual site."
- Truebeck Construction
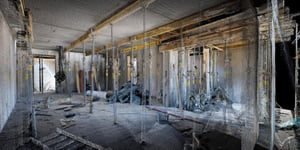
2. Renovation Planning
Renovation planning has also seen remarkable improvements thanks to reality capture technology.
Accurate documentation of current conditions eliminates the guesswork and inaccuracies associated with outdated plans and old-school methods (some tape measure and a camera, for example), ensuring that renovation plans are based on precise data.
"Let's consider a renovation project scenario where the customer possesses only 2D plans, and the job site is located a couple of hours away. With NavVis technology, anyone can take a virtual walk-through and seamlessly navigate between the drawings and the actual site, facilitating easy comparison."
- Truebeck Construction
This level of upfront detail on site conditions prevents possible conflicts and costly modifications during the construction phase, ultimately safeguarding the project’s budget and having a positive environmental impact.
As we will see, applying scanning technology proves invaluable when virtual tours enabled by scanned data allow for meticulous evaluation of a building’s condition without requiring extensive physical inspections. This is especially beneficial for assessing equipment lifespan, identifying necessary replacements, and even creating detailed asset inventories for management purposes.
"The ability to virtually visit the space and facilitate focused discussions on tasks like retrofits or equipment clearances has been immensely popular within the team. This is something they couldn’t accomplish before NavVis."
- Merrick & Company
Reality access technology also aids the process of energy efficiency assessment and subsequent retrofitting. Some projects are even financed with guaranteed energy efficiency savings, with scanning facilitating the evaluation process.
“With NavVis technology, anyone can take a virtual walk-through and seamlessly navigate between the drawings and the actual site.”
– Truebeck Construction
3. Residential and Commercial Building Documentation
Creating detailed and updated documentation for residential and commercial buildings is a critical task that requires both precision and speed. However, gaining physical access to these sites or ensuring uninterrupted work can be challenging.
The use of scanning technology addresses these issues by removing the dangers linked with outdated documentation and the inaccuracies of manual measurements and – when this equipment, like NavVis VLX, is based on advanced Simultaneous Localization and Mapping (SLAM) – by significantly accelerating the process of capturing site conditions, allowing for less disruptive and more frequent scans.
"98% of our scanning is carried out with NavVis VLX, which has drastically improved our scan time and profitability."
– Truebeck Construction
Reality capture platforms such as NavVis IVION provide a seamless connection between point cloud data and photographic documentation, integrating well with commonly used software such as Autodesk Revit for modeling and plan generation. This eases the pain of inconsistent documentation in formats and content and—as we will explore below—makes data exchange among stakeholders a much simpler task.
For effective operation in residential and commercial environments, the chosen reality capture solution must excel in accuracy, speed, and ease of management, creating a balanced and successful combination.
“98% of our scanning is carried out with NavVis VLX.”
– Truebeck Construction
4. Collaboration, Visualization, and Site Visits
When it comes to design, engineering, and construction, transparency is essential. Lack of accurate and consistent information about the progress of a project, along with poor or fragmented communication, can increase the chance of future, expensive reworks.
Adopting integrated scanning and visualization technology such as NavVis facilitates collaboration and planning, enabling remote site visits that circumvent the logistical challenges of assembling teams on-site to assess viability or equipment clearance.
"Bringing together a group of people in one physical space at the same time poses a real challenge. Being able to virtually visit that space is something we couldn't do before. With our clients, we're now considering utilizing this opportunity for emergency management and demonstrating evacuation routes."
– Merrick & Company
Deliverables like 360° walkthroughs offer a great deal of value to clients: they enable a range of stakeholders with different backgrounds and motivations to explore and understand a project site – viewing, searching, and adding spatial information – and provide a single and easily accessible source of truth.
"More than 90% of on-site visits are efficiently avoided… This method optimizes the utilization of as-built data and could potentially eliminate the need for site mobilization and its associated expenses during design and construction phases."
– VHB
"Being able to virtually visit that space is something we couldn't do before."
– Merrick & Company
5. Bidding and Tendering
Accurately estimating the total cost of a construction project, which includes labor, equipment, and materials, based on the documents the client provides during the tendering process, is no easy task.
In tenant improvement (TI) projects involving the renovation of existing buildings, using scanning technology such as NavVis VLX proves beneficial. Any data captured during a site visit or a preliminary job walk can become an integral part of the call for bids or the final project proposal, providing detailed documentation of the site’s existing conditions to support more precise cost estimations. Subcontractors who refine their bids with this method display innovation and trustworthiness, while general contractors who rely on scan data can submit the most competitive proposal to the owner.
This approach allows contractors to compare the point cloud generated on-site with client-provided documentation, revealing discrepancies or inaccuracies and demonstrating the capabilities of in-house technology acquisition and the advantages brought to project implementation.
"The application of scanning technology is particularly emphasized during the preconstruction phase and estimation, serving as a tool for Quality Assurance (QA), Quality Control (QC), and as-built documentation. The intention is to demonstrate to clients the utility of this technology in construction processes, potentially influencing the decision-making process during project selection."
– Truebeck Construction
To sum up, scanning technology is now becoming a key differentiator in the pre-project phase.
6. Preservation, Monitoring, and Claim Management
When construction projects involve historical structures or existing infrastructure and surrounding buildings, contractors are often contractually obliged to protect these items throughout the construction phase.
Implementing preventive measures against potential damage to third-party property and meticulous documentation of the condition of protected items is paramount. Such documentation serves as crucial evidence in resolving any future contractual disputes.
By leveraging reality capture technology, contractors get thorough documentation of each construction phase, providing a clear before-and-after snapshot of critical areas.
Accessible platforms to review and analyze this data facilitate transparent decision-making and the planning of construction activities based on accurate data. All responsible parties are kept informed about the conditions and progress of the construction site, improving coordination and reducing the risk of damage to protected items.