%20(1)%20(1)%20(1).png?width=300&name=2022-07-28-MOTE%20Full%20Bldg%20-%20PointCloudCoord%20(2)%20(1)%20(1)%20(1).png)
IBKS pushes the boundaries of scan-to-BIM with NavVis and PointFuse in a towering project
The firm tested its innovative NavVis and PointFuse workflow in a huge, complex healthcare facility – and succeeded beyond all expectations.
Key takeaways
- IBKS built a fast and accurate scan-to-BIM workflow around two powerful tools with low barriers to entry, NavVis VLX and PointFuse Pro
- The team started delivering complex scan-to-BIM projects in the medical space almost immediately
- Recently, IBKS took on a two-tower, 450,000-square-foot healthcare project in Los Angeles
- With NavVis VLX, each 11-story tower took only 10 days to scan
- With PointFuse Pro, each floor was prepared for Autodesk Revit in only 12 hours
Tall order
IBKS is a digital solutions and management consulting firm offering built-environment services in the healthcare space.
In 2022, IBKS landed a big scan-to-BIM project for a large medical complex on the border of Beverly Hills and West Hollywood in Los Angeles. This site sprawls over 375,000 square feet — covering multiple medical suites and two 11-story towers. Including exterior elements, the sum balloons to over 450,000 square feet.
It was the biggest scan-to-BIM project undertaken by IBKS to date. It was also a huge test for the firm’s innovative scan-to-BIM workflow, which they had recently built around the NavVis VLX 3D laser scanner and PointFuse Pro software.
.png?width=300&name=2022-07-28%20_MOTE%20Full%20Bldg%20-%20MeshCoord%20(1).png)
Innovate out of the gate
According to Mo Haidar, founder of IBKS, the firm had added only recently reality capture to its services portfolio. IBKS had some in-house scan-to-BIM experience, but much of it was five years old — or even older — so the main players were essentially starting fresh.
This proved to be a strength rather than a weakness. IBKS was able to build an innovative workflow with no preconceptions about the “best” tools to use.
As Haidar explains, IBKS “did research for every device that’s out there, and quickly realized that our use case would require a mobile mapping approach. And we pretty much knew that it was going to be the NavVis Reality Capture Solution: NavVis VLX and NavVis IVION. It was obvious because they offered no barrier to entry and no intimidation whatsoever.”
Spivey Lipsey, digital twin solutions lead with IBKS, adds that the mobile-mapping solution wasn’t just beginner friendly, it also met the firm’s stringent technical requirements for work in healthcare.
“We were looking for a fair amount of accuracy, but we also have a lot of square footage to cover. The scanner hit that sweet spot of accuracy and speed.”
![]()
- Spivey Lipsey, Digital Twin Solutions Lead, IBKS
To complement their NavVis solution, IBKS looked for a downstream scan-to-BIM tool that offered a similar combination of a low barrier to entry, speed, and data quality. They found it in PointFuse Pro. This software would automatically classify surfaces, generate meshes of their point clouds to reduce file size, and produce LOD 200 models rapidly. And it would be very easy to use.
Lipsey says the most important factor, however, was that IBKS could be sure the tools would hang together as a complete workflow.
“Someone that begins their adventure into this space — as they’re trying to procure software and hardware for their solution — they quickly understand that there is a very convoluted world of software versions and compatibility issues. And many of the software solutions are counterintuitive.”
“A big selling point for me,” he adds, “is that NavVis and PointFuse already had a collaboration. That lent a degree of confidence that these tools would work together.”
With the right tools in place, IBKS then worked with the technical teams at NavVis and PointFuse to hone the workflow over a handful of large scan-to-BIM projects. The firm used these jobs to develop best practices for maintaining consistency, capturing corridors without drift, organizing data, auto-recognizing elements, and more.
The big test
Then, IBKS landed the scan-to-BIM project for the two-tower complex in Los Angeles, and put their workflow to its biggest test yet.
This 450,000-square-foot project presented a number of challenges. IBKS would need to capture data that was accurate enough for a BIM model that met customer specs. And, since the site was an active medical facility, they would need to work quickly after hours to reduce disruption to the staff.
As mentioned earlier, the project’s scan area sprawled across multiple levels of medical suites and 22 floors total. But there was still one more level of complexity: The end client didn’t own the buildings being scanned, so IBKS could only capture the areas their client had leased.
This meant the scans would be scattered — Haidar has called the arrangement “Swiss cheese.” The team was uncertain if their software could maintain proper alignment through the processing chain.
“We were worried that we might need to do the alignment of the multiple levels in two places, NavVis IVION, and PointFuse Pro, and the last thing you want to do is the same task twice.”
![]()
- Mo Haidar, Founder, IBKS
NavVis VLX and NavVis IVION
Lipsey says that the team accelerated the mobile-mapping workflow by capturing numerous smaller scans without the use of control points. This enabled them to get in and out of each space very quickly while reducing drift to maintain a high level of accuracy.
To combat any possible alignment problems that might arise due to the scattered layout, IBKS arranged the scans in a “tree” configuration.
“There were two stairwells in each tower that were the full height of the building,” Lipsey says. “So, we scanned those individually. We also scanned each corridor for each floor, as well as the restrooms, and a portion of the stairwell. Then we scanned the suites individually.”
When it came time to process, the team performed initial alignment work in NavVis IVION. “We were able to connect the corridor to the stairwell and align the levels like a tree trunk with branches,” Lipsey says. “Then, we aligned the suites to the corridor.”
Next, the team used the crop and download tool to export each level individually.
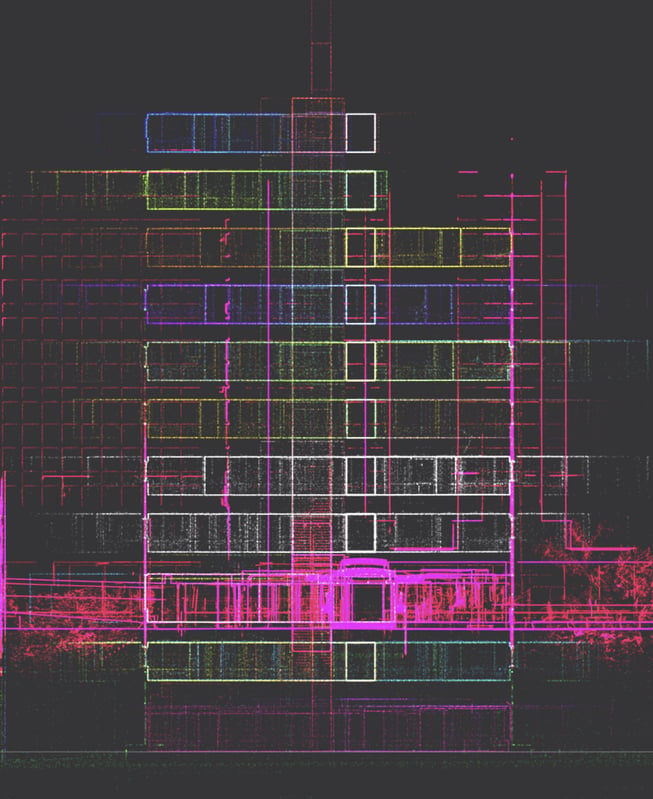
%20-%20Copy.png?width=694&name=1-%20PFP%20CLASSIFIED%20MESH%20MODEL%20FULL%20BLDG%20(MOTE)%20-%20Copy.png)
Processing: PointFuse Pro and Autodesk Revit
Then, they passed the data along to PointFuse Pro. The transition was seamless. “We brought each level, each combined data set into PointFuse Pro. They stacked up exactly as we had aligned them in NavVis IVION with no need for further alignment.”
Eliane Bouery, BIM Consultant with IBKS, says the next step was to begin processing. She used PointFuse Pro to automatically generate a mesh and classify large planar surfaces like walls and floors.
“Next, floor by floor, we did the classification of elements,” she says. She navigated inside each individual room and verified or identified doors, walls, furniture, windows, and other important elements. Meanwhile, she kept the original point cloud open in NavVis IVION as a visual reference.
“After that, we went to the BIM Space Management module and produced a 3D model automatically. Then I just adjusted and positioned each window and door. I worked in parallel in NavVis IVION, navigating to each room and streaming the measurements to verify positioning.”
After she completed the alignment of each floor, she exported an IFC file from PointFuse Pro to easily upload into Revit for the final clean-up and modeling, again with no need for further alignment. From there, the BIM model was quickly completed to the client’s specs.
NavVis to PointFuse to Autodesk Revit Workflow
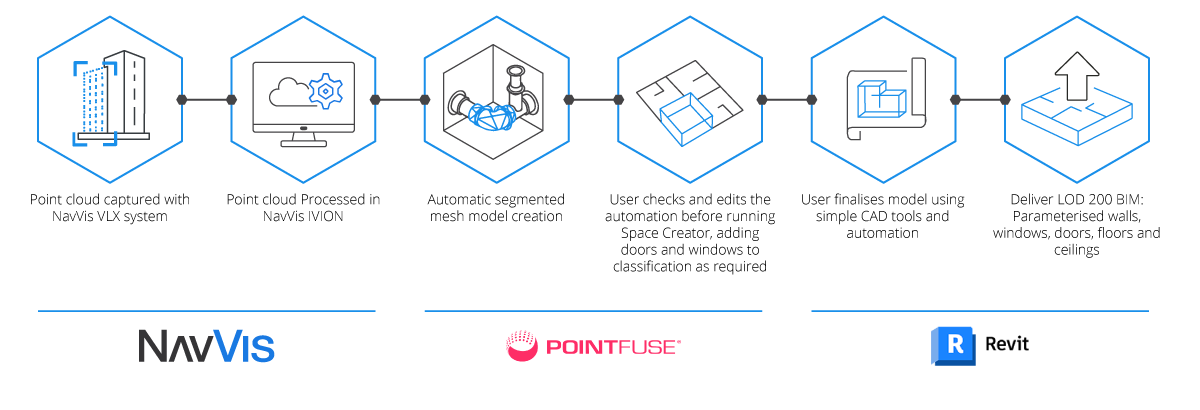
Big success and a future outlook
IBKS says the NavVis and PointFuse workflow exceeded expectations and made what was initially a daunting task, very easy and smooth.
For one, the mobile scanning was fast. The team was in and out of each tower in only 10 days and were happy that they didn’t need to return after the initial capture.
The speed of the mobile mapping workflow also helped reduce disruption to the medical personnel on-site. “Even though we scanned after hours, there were doctors and nurses in some of the offices,” notes Haidar. “And they had to step out for only three minutes for us to complete the scan and get back. To them, it was like a welcome coffee break. Almost everybody was surprised by how quickly we got out of their space.”
And that speed didn’t mean a drop in accuracy or data quality. “We’re actually seeing some really high precision using mobile mapping in spaces like long corridors,” says Lipsey. “And apart from just a few very minor artifacts, everything came out really clean. I think we’ll be able to use NavVis VLX on a much larger scale than we anticipated.”
As for the software workflow, Lipsey says it was definitely up to the challenges posed by scan-to-BIM work for large medical facilities.
NavVis IVION reduced the initial processing time to 4 hours per floor (roughly 16,000 sq feet). PointFuse Pro reduced the “scan-to-Revit-model” time to only 12 hours per floor. It also reduced the size of the point cloud files by over 66%, saving a lot of storage space and speeding up transfers significantly.
IBKS’ innovative workflow also managed the complex alignment with no problem. “In fact, I think it enables us to do as many stories as we need,” says Lipsey. “We could start with alignment in NavVis IVION, bring the data accurately into PointFuse Pro, and then Revit, without having to do any further translation.”
“This is a great testament to how both of the products work together,” concludes Haidar. “We’ve seen some tremendous success here.”
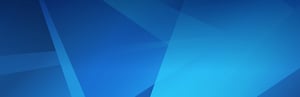
Next generation 3D laser scanning is here
Wearable, 3D laser scanning devices are faster and more scalable than ever before, providing survey-level data quality for even the most demanding projects.
Find out how our entire reality capture solution can benefit your scan-to-BIM workflows by chatting with one of our experts: