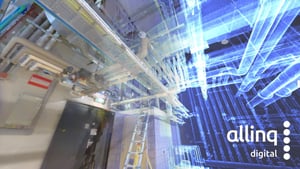
Schiphol Airport and Allinq Digital transform scan to BIM to realize ambitious sustainability goals
A leading AEC service provider used NavVis tech to execute a series of ambitious scan-to-BIM projects at Amsterdam’s international airport.
Key takeaways
- Allinq Digital won Schiphol’s point cloud challenge in 2019, kicking off a series of scan-to-BIM projects for the airport
- Recently, the firm used NavVis VLX and in-house automated modeling software to model over 300,000 square meters of the airport
- This workflow reduced the price per square meter by 68%
- After this successful scan-to-BIM project, Allinq Digital won the contract to model all of Schiphol Airport in December 2023
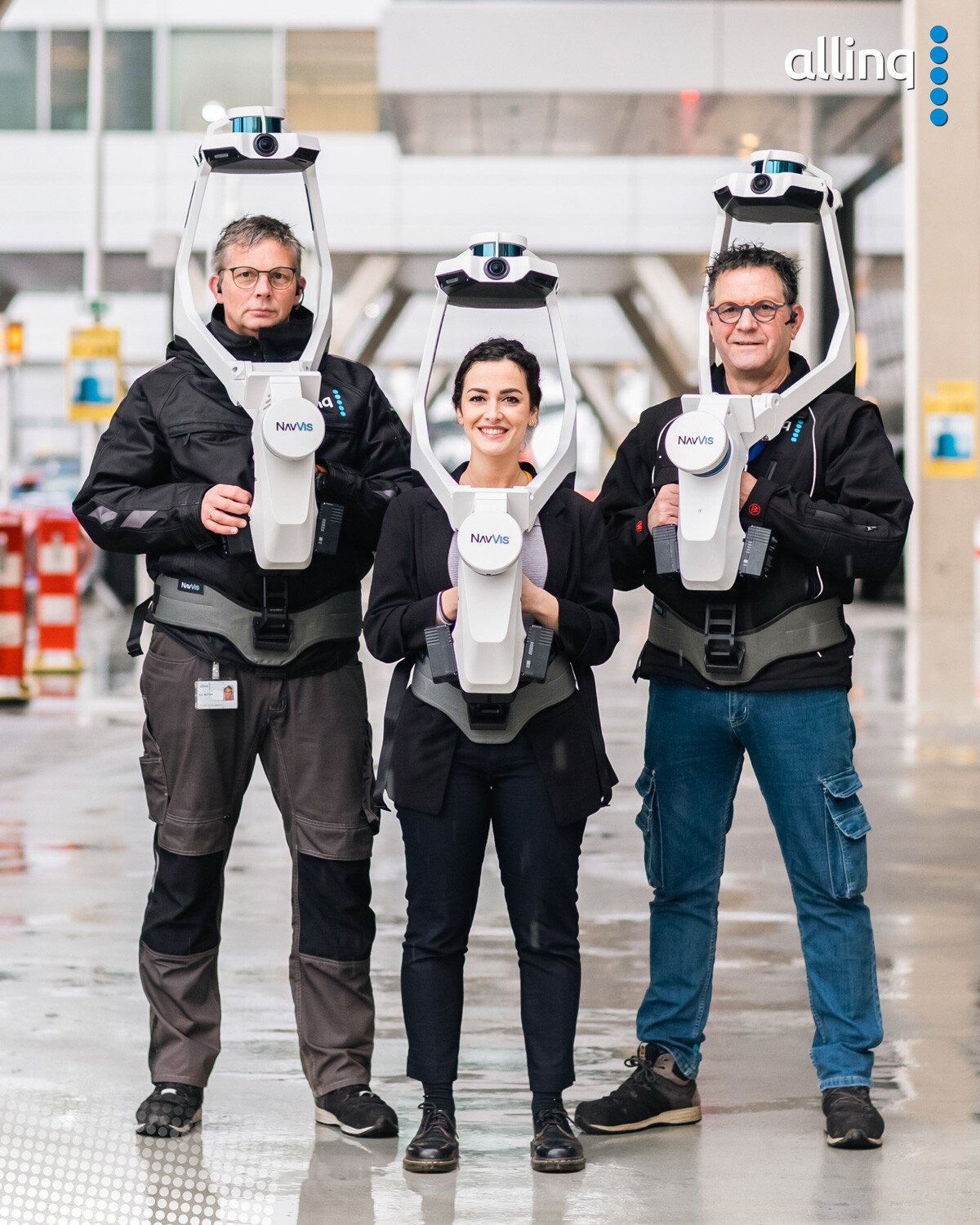
You could call Allinq Digital “innovative,” but that would be faint praise.
Established as part of the Allinq Group under the leadership of Leander Goor, Allinq Digital specializes in delivering digital services such as scan to BIM for AEC customers. The firm is committed to keeping a majority of its operations within the Netherlands, which inspires forward-thinking approaches to technology as a way to reduce labor costs.
In this two-part case study, we’ll explore Allinq Digital’s technological innovations. In this first part, we’ll see how the firm has transformed its scan-to-BIM workflow with wearable laser scanning technology and automated modeling software.
In particular, we’ll look at a series of projects Allinq Digital performed for Amsterdam Airport Schiphol. Here, Goor and his team used NavVis wearable laser scanning systems and some clever in-house tools to reduce the cost of BIM modeling, help the airport take on projects that were impossible before, and even lay the groundwork for a forthcoming AR wayfinding application.
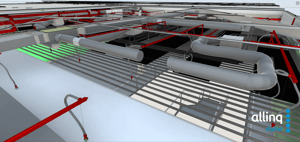
Mini case study: The Schiphol Point Cloud Challenge
Allinq Digital first collaborated with Schiphol when the firm took on the airport’s Point Cloud Challenge in 2019.
The airport organized the challenge because they wanted to explore the value that could be derived from comparing multiple point clouds taken in the same space over time. To that end, they invited companies across the Netherlands to delve into 3D data sets captured by the airport, perform analysis, and present their insights. The competition focused on one particular terminal that was undergoing partial reconstruction at the time.
Allinq Digital began by conducting a comparative analysis of two point clouds taken at different times in order to detect what had changed between the captures. Then, they updated the Revit model accordingly to maintain Schiphol's extensive asset records.
The team also proposed a more innovative solution for keeping the model up to date in the future. They observed that the airport was equipped with various other sensors capable of capturing geometry. Why not leverage those as well?
"We suggested that instead of daily scanning, which would be time-consuming and generate massive amounts of data, they opt for a one-time scan using the NavVis M6," Goor said.
"We would generate a high-quality Revit model and use the other sensors around the airport to keep it updated. Allinq Digital would employ our own in-house object-recognition AI and Dynamo scripts to identify what objects had changed and what objects had been added, and then place them accurately in the Revit file. This would facilitate more effective tracking."
Schiphol was impressed by this idea — so much that Allinq Digital won the challenge. This marked the initial step in an ongoing partnership between the company and Schiphol to find innovative methodologies and achieve ambitious sustainability goals.
Want to learn more about how you can optimize your scan-to-BIM workflows with 3D laser scanning?
Technical scan-to-BIM
As part of Schiphol’s mission to reduce its environmental impact, the airport is currently replacing a significant portion of its equipment with eco-friendly alternatives. The renovation plan leverages BIM methodology, enabling the team to plan construction work meticulously and reduce impact on passenger operations — another one of the airport’s highest priorities.
To that end, Schiphol tasked Allinq Digital to work with one of the airport’s primary contractors to scan technical rooms and generate BIM models at both LOD 300 and LOD 400.
This is no simple task. As Goor explains, the technical rooms are densely packed with infrastructure for power, water, sewage, and air. They contain piping, heating elements, plumbing fixtures, sprinkler heads, 19-inch cabinets filled with switches and routers, and even industrial-scale humidifiers.
This complexity results in small spaces and a high risk of blind spots in the final scan data.
Moreover, there was a large number rooms to capture. The airport has approximately 50,000 square meters of technical rooms, varying in size from 100 to 3,000 square meters. Time was also limited, with Schiphol only able to allocate a few hours per room for Allinq Digital to conduct the scans.
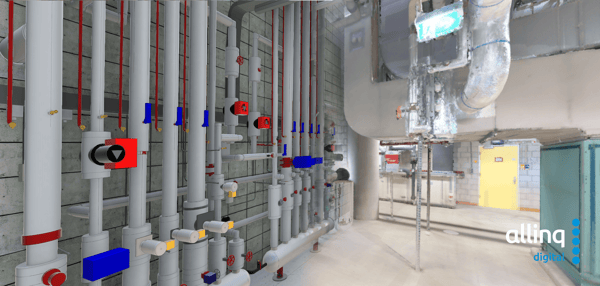
The traditional method
From the outset, Schiphol understood that they could not use traditional methods for BIM modeling without disrupting airport operations for passengers.
The traditional approach involves manually generating as-built drawings of a project. For example, if the airport had added a pipe, a technician would visit the site, use a tape measure to gather dimensions, and record them on paper. Then, they would model it in CAD.
This method is less than ideal, Goor argues. "When an engineer needs to modify the piping, they update the drawing again. This iterative process leads to inaccuracies over time, resulting in problems.”
Allinq Digital recognized that Schiphol would benefit from digitizing their workflow — but they also knew that traditional TLS (terrestrial laser scanning) wouldn't suffice.
"We had only a limited timeframe to scan these highly complex rooms,” he says. “TLS takes too long due to the numerous blind spots that need to be addressed. Since we aim to minimize disruption to passengers, speed is crucial."
To solve this problem, Allinq Digital collaborated with Schiphol to explore other methodologies for capture. Ultimately, they opted to use a latest-generation wearable laser scanning tool: NavVis VLX.
Enter NavVis VLX and NavVis IVION
Goor and Allinq Digital were familiar with NavVis tech, and confident that the wearable laser scanning system was up to the task.
A few years back, following Allinq Digital’s participation in the Schiphol point cloud challenge, the firm had demoed the NavVis VLX 2. Like most scanning service providers would, they put the system to the test in a real-world scenario. They benchmarked its speed for capturing rooftop antennae for a telecom project.
"It outpaced TLS significantly," Goor recalls. "And the data quality exceeded our expectations. However, what truly impressed us was NavVis IVION. This played a significant role in our preference for the system. Unlike other competitors who primarily focus on hardware, NavVis feels more like a software company that also manufactures hardware."
"I could tell that NavVis had prioritized the platform, as they had made it incredibly user-friendly. The added benefit was the ability to navigate through the data with NavVis IVION and quickly take measurements, which proved invaluable for our project."
Following the successful trial, Allinq Digital acquired three NavVis VLX 2 units. They also acquired the first NavVis VLX 3 in Benelux, with plans to use it for capturing the technical rooms at Schiphol.
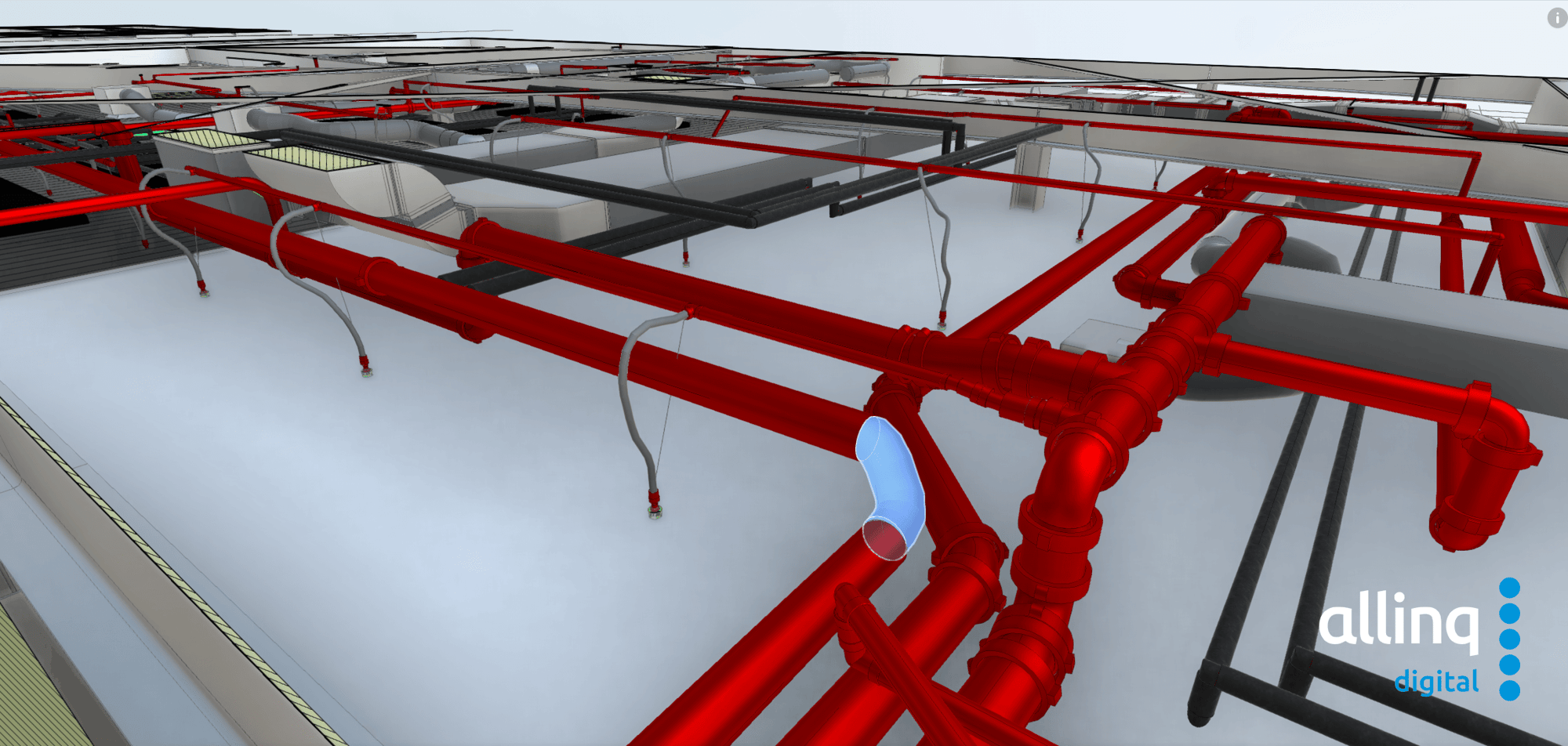
Automating a workflow
Goor says that he utilized a "standard" scan-to-BIM workflow to model the technical rooms. That's not entirely accurate: Allinq Digital’s innovation was on display in this part of the workflow as well.
Initially, the team established ground control throughout the technical rooms using stickers or fixed points, which they captured with a total station. Then they scanned with NavVis VLX 3, ensuring comprehensive coverage by capturing panoramic photos and maneuvering around occlusions. For areas that required scanning above a height of 8m, they used a TLS for spot capture.
Here's the most ingenious aspect: After processing the point clouds in NavVis IVION, Goor and his team imported the data into Allinq Digital’s proprietary auto-segmentation tool. This expedited the process by identifying Revit elements within the point cloud automatically.
"We run scripts to detect elements based on point cloud segmentation and our library of elements,” says Goor. “Then, we insert references – such as measurements – into the model. We create a section box and instruct the Autodesk Dynamo player, the script behind it, to position the model."
"This process has streamlined our workflow to the fullest extent possible. When implemented, we can generate a Revit model rapidly."
Density, speed, and savings
Goor was particularly impressed by the performance of the NavVis VLX 3, which surpassed even the NavVis VLX 2.
“The NavVis VLX 3 had higher point density, resulting in more detailed point clouds in these intricate technical rooms. Additionally, there were minimal differences compared to our FARO scanner at 5 minutes per scan, especially within a range of 10 meters. The data quality provided by the NavVis VLX 3 exceeded our expectations."
Allinq Digital's workflow was not only faster, but also significantly less expensive than traditional scan to BIM methods. Using NavVis VLX 3 and the automated modeling process led to an impressive 68% reduction in Schiphol's overall scan-to-BIM expenses.
Without this approach, it would not have been economically viable for Schiphol to use laser scanning for the renovation project. The airport would have been compelled to use traditional methods, resulting in a more pronounced impact on the passenger experience.
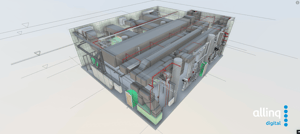
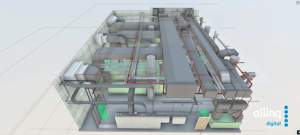
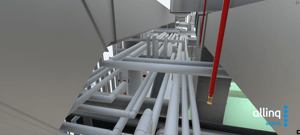

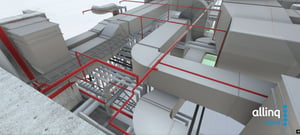
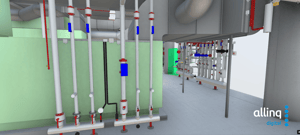
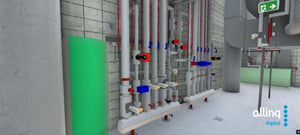
A partnership takes off
Allinq Digital delivered the BIM models to the airport and provided Schiphol with three months of access to IVION. According to Goor, Schiphol was highly satisfied with the deliverables and "were so impressed with NavVis IVION that they obtained their own enterprise subscription."
Schiphol also appreciated the user-friendliness of the NavVis VLX hardware. "The airport discovered that any regular staff member could use the scanner to conduct a quick scan for quotation purposes and then share it on IVION with multiple parties," explains Goor. "Now, they can generate a quote rapidly and easily, eliminating the need for multiple companies and complex equipment to perform a site survey."
Overall, NavVis VLX has introduced a range of new potential use cases for Schiphol.
"Thanks to NavVis VLX 3, NavVis IVION, and our modeling methodologies,” says Goor, "we reduced the airport’s cost for scan-to-BIM by 68% per square meter. Now, it's financially feasible for Schiphol to work on many projects that require a high-quality digital twin of the terminal building. After seeing the success of this workflow, Schiphol immediately began exploring new challenges to continue our collaboration."
Stay tuned for Part 2: Allinq Digital scans 250,000 square meters of parking garages for a construction project – and lays the groundwork for an unprecedented AR wayfinding app.
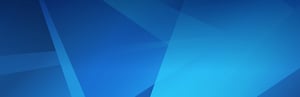
Next generation 3D laser scanning is here
Wearable, 3D laser scanning devices are faster and more scalable than ever before, providing survey-level data quality for even the most demanding projects.
Find out how our entire reality capture solution can benefit your scan-to-BIM workflows by chatting with one of our experts: