What is factory planning? How does it differ from production planning or layout planning? A primer on optimizing the space where manufacturing takes place.
Congratulations! Your spanking-new factory building is now ready. It’s probably quite a simple construction: a poured concrete floor, four walls, and a roof, with electricity and water connections.
But you can’t manufacture products in an empty shed. Before you can start using it as your production base, you’ll have to do install everything you need to make your products. Welcome to the world of factory planning.
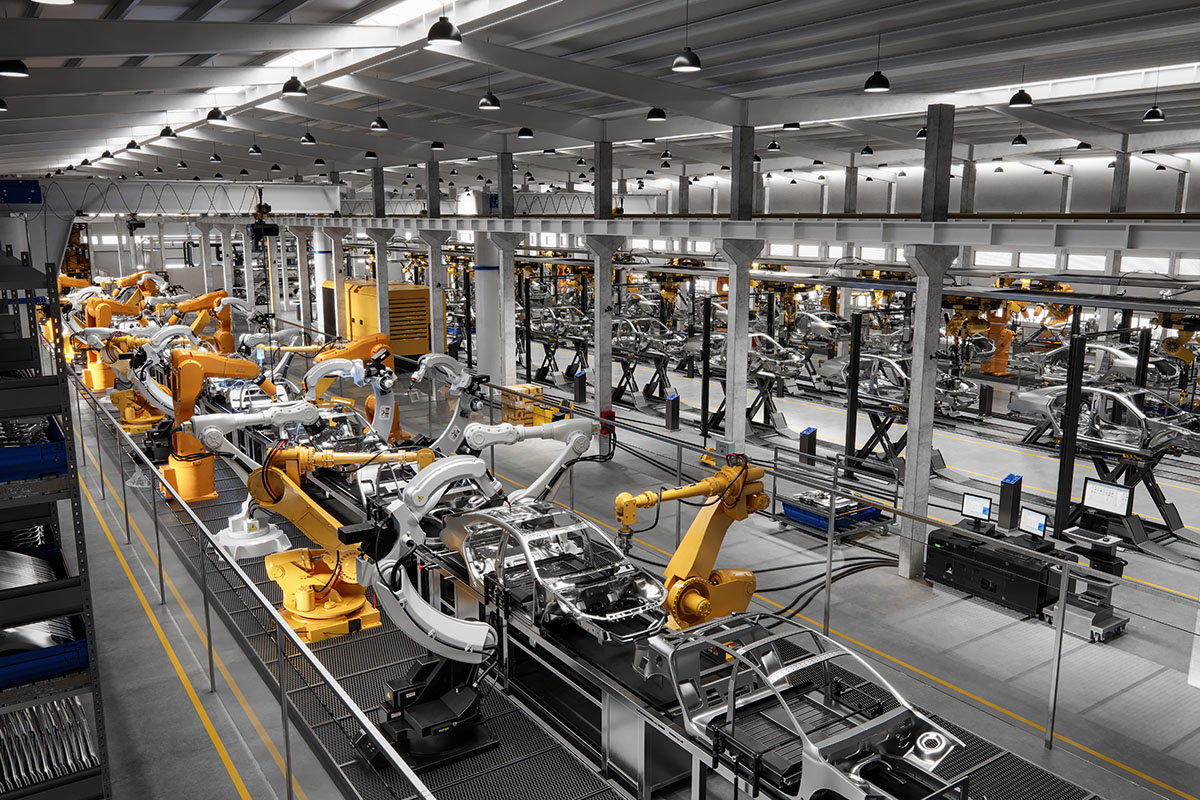
How a factory makes its products
Most manufacturers embarking on factory planning will already have a fairly detailed idea of how they will make their products:
- They will have to bring in raw materials and/or components.
- There will be a number of discrete stages in which these will be turned into the form necessary for incorporation into the product, and this may involve machinery.
- There will be assembly stages, which might be carried out by human operators or robots.
- There may be a finishing stage, such as polishing or painting.
- The final product will need to be checked to ensure that it meets all the quality criteria for shipping.
Plus, everything will need to be transported between all the stages outlined above.
But merely knowing these facts does not mean that the new factory owner will be able to design the best way of arranging the space inside the factory shell and installing all the equipment needed. To achieve this, the help of a specialist factory planner may be needed.
Understanding the space where manufacturing takes place
The first task of a factory planner is typically to fully understand the space in which manufacturing is to take place. Perhaps they’re already familiar with the location, but they want an update on the current conditions of the site.
This will include the dimensions of the space, the locations of any structures which already occupy it and needs to be accommodated in the factory design, such as pillars or columns or trusses supporting the roof, where power, water and other utilities may be brought into the site, and the access points for people and materials.
To accurately determine these vital points, indoor mapping technologies such as laser scanning to obtain point-cloud data may be used, and the results uploaded into the Computer-Aided Design (CAD) packages that will invariably be used to design the equipment layout.
Also important is to understand the product being manufactured, the complexity of which will determine what the factory layout ultimately looks like.
The production process must be broken down into its various stages and each must be understood on a detailed and technical level.
For example, if metal needs to be shaped into specific forms for carmaking, there are questions like:
- Will this be done by bending sheets, grinding blocks, drilling holes, or a combination of all of these?
- Will these tasks be accomplished using multi-functional machine tools or will people be using the appropriate tools to do them by hand?
- When it comes to joining opponents together, will they be welded, glued or joined using mechanical means, such as rivets, screws or bolts?
- Is a clean electrical connection required?
- How accurate do all these operations need to be?
In each case, the appropriate space needs to be reserved for the machines or workbenches, the appropriate equipment selected and the necessary utilities brought to the location.
The differences between production, factory, and layout planning
It’s important here to make a distinction between factory planning, production planning and layout planning – three terms which are sometimes used interchangeably.
Production planning tends to be a short-term process, focused on the day-to-day operation of an existing facility, ensuring that it is running smoothly and meeting the commercial objectives of the operator.
Factory planning is a medium-to-long term process, focusing on the physical properties needed for the facility to fulfil its function, and includes specification of equipment; its scope also includes modifications that may be needed to the factory when it is in operation.
Layout planning is smaller in scope, focusing more tightly on the simple matter of what (and who) goes where.
Standardized modules in the production process
The individual steps that comprise a production process are usually treated as modules. For example, manufacturing a car will encompass a propulsion module, a fuel module, and a control module for the driver (which is contained within a larger passenger module).
Specialist software includes digital models of factory schematics, into which specific parameters such as the key performance indicators required by the factory operator can be input.
These models allow the factory modules to be designed at various levels of detail – starting, for example, as a simple block indicating which operation is being carried out and increasing in detail to specify the precise type of machinery being used, the locations of operator stations, and the transport infrastructure to bring materials and components into and out of the module.
The modules can be linked together in a flowchart-like schematic, which in turn can be translated into a layout structure, simulating the physical form of the factory.
Today, this is usually done using three-dimensional digital renders to produce a near-realistic graphic of the factory, which can be “flown through” and in which the specifications of each piece of equipment can be embedded.
Linking representational modules to their technical parameters in a graphical, clickable form is a hallmark of building information management (BIM), a form of design software more commonly associated with architecture and the construction industry, but which has obvious utility in factory planning.
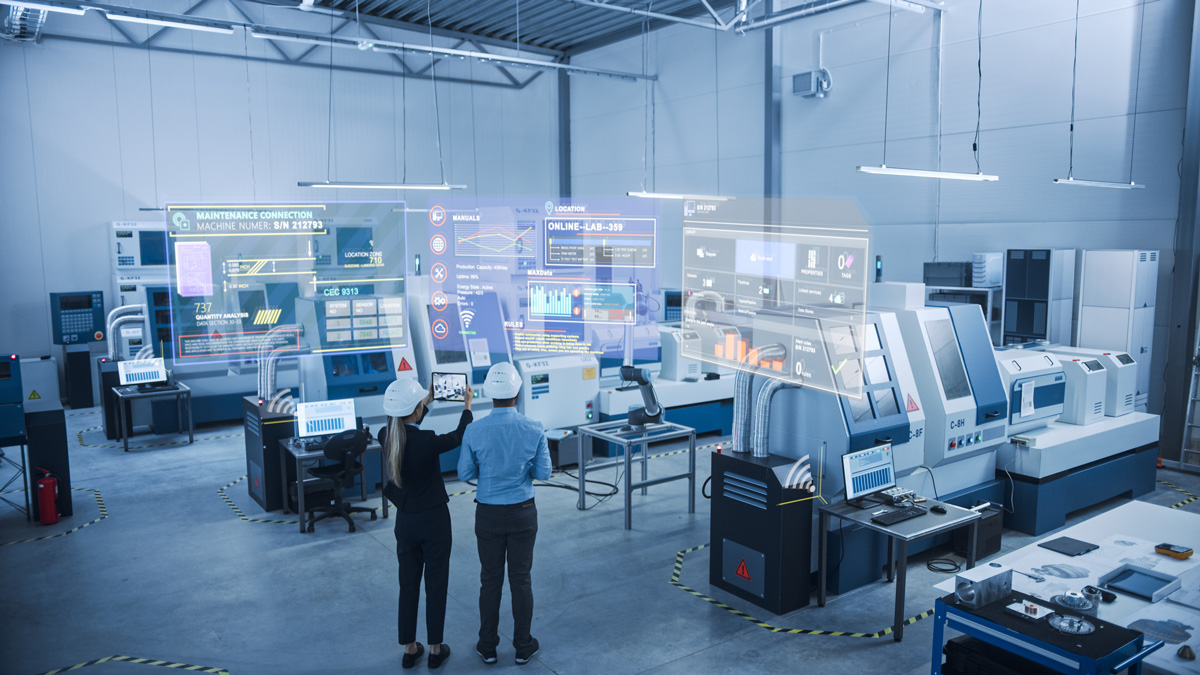
Fusion for the future
Establishing a graphical model of a factory in which the technical parameters of each piece of equipment are linked to their representation is a component of a model known as a digital twin, and these are not just useful for design.
When a production facility is operating, the working data from each machine can also be linked to the representation – showing, for example, the shaft speed and cutting head temperature of a machine tool – thus making what may have started as a design tool into a vital part of the factory’s operating control and instrumentation suite.
BIM can be a part of this. In a paper presented at a conference in September 2021 in Spain, researchers from the laboratory for machine tools and production engineering at RWTH Aachen University argued that cost increases and time delays caused by poor communication between different factory planners could be eliminated if all the planners used a standardised BIM approach throughout the project.
Automotive manufacturing companies use technology like NavVis mobile mapping systems to create point cloud models of its factories, and imports these models into software such as Revit (a BIM system widely used in architecture) and Catia (a well-established CAD package) so that different teams of planners can work together on the design project.
Wrapping up
So there you have it, a high-level overview of the core concepts in factory planning, the multiple considerations at play, and potential developments for the future.
For a deeper dive into how factory planning is achieved in modern car manufacturing, read an interview with Paul Hänchen, Senior Solution Manager, Digital Factory, where he explains current practices and how they can be enhanced with reality capture solutions.
In the meantime, would you like to learn more about the NavVis Digital Factory Solution? Contact us for more information, or download a copy of our free guide to getting started with your digital factory implementation.
Stuart Nathan is a London-based freelance science writer, formerly features editor for The Engineer. He has written for publications including The Economist 1843, Ingenia and MIT Technology Review. He believes that without good communication, the full potential of science and technology cannot be realised.